Paul Richards, Bill Goretkin, Wireless Sensors
There is a proverb that “it is impossible to control things beyond the scope of the ability†and is very suitable for applying to energy and industrial process optimization. The data needs of these industries are driving the rapid adoption of wireless sensors and connecting them to gateways for the Internet of Things (IoT). This type of gateway enables the transparency of past details of opaque operations by allowing the deployment of low-cost sensors. With the application of advanced analytics, the advantages become more pronounced.
But there is a major challenge in achieving these advantages. Companies need to determine the best way to connect legacy systems that are not IP-friendly communication protocols (such as Modbus RTU) isolation.
This article explores a solution for Wireless Sensors, which connects sensors in a self-configured and self-healing wireless mesh network with Intel® NUC-based IoT gateways and cloud communications (Figure 1). We describe how this solution combines the flexibility and resiliency of mesh networking with the low latency of a star topology. We discuss how the IoT gateway supports RESTful Web services and integration with the Microsoft Azure platform to provide seamless data paths for cloud and advanced analytics. We also consider the advantages of using Intel® NUC with a crop networking gateway platform.

Figure 1. The Wireless Sensors solution is a self-configured and self-healing wireless mesh network using Intel processor-based IoT gateways.
The toughest mile
The most difficult part of connecting to the Internet of Things is often the "last mile" between the local Internet connection to the point where the device or system is located in the facility. Connecting these "devices" means getting existing sensors online and acquiring, configuring and connecting new sensors.
Surprisingly, the best way is not to fully implement Internet connectivity. Cheaper methods can often achieve the same functionality, and there is no complexity to add hundreds or thousands of new IP addresses.
A radio frequency (RF)-based mesh network combined with a powerful IoT gateway provides an inexpensive method. For new and existing operations, wireless mesh sensor networks provide suitable scalability, redundancy, and ease of deployment. Since no wires need to be installed, such networks can start working within hours. The network connecting the cloud through the IoT gateway provides all the technologies needed for data collection and cloud communication.
Use mesh timing
To better understand the benefits of wireless mesh networking, consider alternatives. Most wireless IP networks use a star topology, and all nodes communicate directly with the network through devices such as IoT gateways. If the end-to-end transmission time is critical, this type of direct communication path can be provided. However, star topology often lacks fault tolerance, so this advantage comes at a price. Network expansion in large buildings or outdoor areas is also more difficult.
Mesh topology provides a convenient solution for applications that can tolerate certain delays. In this topology, data is forwarded between nodes until it reaches the intended final destination. If a separate transmission segment is temporarily unavailable, the data will automatically re-adjust the path on the alternate path. The ability to recover from a single point of failure significantly increases overall reliability.
Mixed solution
For applications that require both – star and mesh – best advantage, Wireless Sensors offers a hybrid solution based on SensiNet* technology. The SensiNet implementation of Wireless Sensors, proven effective for data center environmental monitoring, takes advantage of the low latency of the star topology while maintaining the flexibility and resiliency of the mesh approach (Figure 2).

Figure 2. The SensiNet implementation of Wireless Sensors provides low latency in a star topology while maintaining the flexibility and resiliency of traditional mesh networking.
Reasons why this technology is a hybrid technology include:
• As in the star topology, bridging (and its corresponding routers) provides a direct link to the IP network.
• As in mesh networks, sensors connect to routers and bridges just like ordinary nodes, and automatically rescale to different routers or bridges if transmission segments are not available.
The availability of continuous network traffic provided by the solution's RF mesh router and bridging is an important advantage. In traditional mesh networking, the network processes messages only when the plan evokes it. With mesh routers and interrupt-based messages, SensiNet continues to be available for immediate delivery of communications.
SensiNet's hybrid approach also supports separate selection of reporting intervals. Since the entire network is not subject to the most time-sensitive measurement management, each node can be set to optimally combine reporting intervals with battery life.
Greater flexibility
If a critical node loses power after a large amount of communication runs out of battery power, traditional mesh networks often crash. SensiNet avoids this problem by ensuring reliable communications over redundant communication paths. Self-organization and self-healing capabilities allow SensiNet to adapt to changes in the physical environment and contribute to its resiliency. In the event of interference, the network can also be dynamically reorganized to coexist with other networks.
New and traditional sensors
To help companies quickly cross the last mile and connect legacy equipment, Wireless Sensors offers its own line of smart sensors and accessories for fast facilities (Figure 3). Sensors address applications ranging from smart buildings and data centers to central industrial applications such as cryogenic storage. Sensors can be used in: ambient and enclosed environments, humidity, pressure, differential pressure, air flow, contact state, and AC current. As monitoring needs change, sensors can be easily reconfigured and repositioned.

Figure 3. Wireless Sensors offers an attractive array of smart sensors for a variety of uses and environments.
For sensors that measure environmental conditions, Wireless Sensors constructs its device to allow increased air flow. High-performance embedded MEMS sensors respond quickly to changes. The wall mounting bracket is easy to install and the C battery provides a significantly longer life.
To integrate traditional analog third-party sensors, Wireless Sensors feed the system with 4-20 mA and 0-10 VDC inputs on the smart sensor. The smart sensor then communicates with the wireless IoT gateway via a bridge.
From RF to IP
In SensiNet mesh networks, sensors exchange EF packets. To implement IoT communications, bridging in the network translates these RF packets into TCP/IP packets. A single bridge can support integration of hundreds of sensor nodes, reducing costs. Remote bridges can support hard-wired sensors if the application requires only a few measurement points. By distributing bridging over the Ethernet network, the network can easily handle hundreds of sensors, leveraging the scalability and modality of Ethernet (wired, Wi-Fi, cellular networks).
Two wireless gateway options
To collect data from the bridge and connect to the cloud, Wireless Sensors offers two wireless gateways: GWAY-2100 and GWAY-2105. Both support applications and are based on the Intel NUC supported by the Intel® AtomTM processor E3815.
The gateway includes network management, user interface, data logging, trending, alarming, and communication capabilities. To access and configure the system, only a standard browser and network connection is required. No other software is required.
Both gateways provide the same extensive protocol and network support. Wireless Sensors recommends the GWAY-2100 for smaller applications and as an independent data recording device with real-time views, trends, and email alerts (Figure 4). Onboard can store up to 8 million records and the system will automatically send sensor data over common protocols.
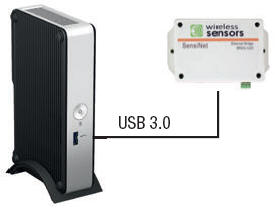
Figure 4. The Intel NUC-based GWAY-2100 Wireless Gateway (shown BRDG-1222) is an application support design for smaller applications.
GWAY-2105 can connect to larger existing network architectures by supporting up to 5 remotely installed SensiNet bridges (Figure 5). It implements an integration point for sensors around the building, inside and outside the campus, or around the world. GWAY-2105 provides the same protocol and network support as GWAY-2100.
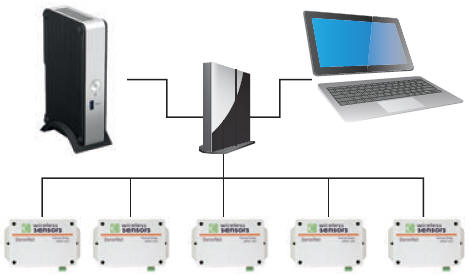
Figure 5. GWAY-2105 supports larger existing network architectures by connecting up to five remotely installed SensiNet bridges.
Middleware on the gateway extracts a single sensor from IP complexity, allowing easy integration of sensors and IoT with modern communication protocols. The gateway also provides a platform for data buffering, edge analysis, and central alarms to reduce cloud processing and storage costs.
The gateway's onboard Web server implements edge-to-cloud communication. Extensive protocols including Modbus, SNMP, ODBC, OPC, HTTP POST, SOAP, and FTP support simple integration (Figure 6). After connecting all devices, users can remotely view reminders and monitor trends. Alternatively, the system can forward the collected sensor data to the control and enterprise network through the gateway.
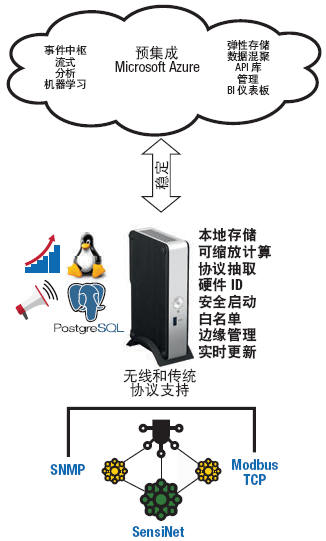
Figure 6. The gateway onboard Web server provides extensive protocol support to simplify integration.
Based on Intel® NUC
The Intel® NUC Kit for creating these gateways is a compact tool for companies and organizations that value value. This low cost solution offers:
• Fanless design for quiet and reliable
• Intel® AtomTM Processor E3815 with 5 W Thermal Design Power (TDP)
• 4 GB on-board embedded MultiMediaCard (eMMC) storage
• Internal flat panel display cable for built-in screen
• Video Graphics Array (VGA) port for monitor compatibility in traditional installations
• Inter integrated circuit (I2C) and pulse width modulation (PWM) signals for connecting sensors and other IoT-enabled embedded devices
With industrial design and support for Linux* and Windows* embedded operating systems, Intel NUC with Intel® AtomTM processor provides performance, low power, low price, and software compatibility for gateway applications. A built-in watchdog timer that provides high cost shutdown protection for high availability resiliency. In addition, Intel NUC uses a separate Trusted Platform Module (TPM) for hardware-based data encryption to protect confidential information.
Intel NUC with a more powerful Intel® processor allows the solution to be used for more complex data analysis or data adjustments. These processors include higher performance Intel Atom processors, as well as the latest Intel® Celeron®, Intel® Pentium®, and Intel® CoreTM processors. The latter uses SKUs to provide the security and manageability features of Intel® vProTM technology.
Analysis Gateway
The Wireless Sensors configured Intel NUC IoT Gateway is pre-integrated with the Microsoft Azure platform to enable seamless data paths with advanced analytics tools in the cloud. Azure IoT Services, a set of Microsoft cloud services, supports extensive resource monitoring and data analysis, resulting in improved efficiency and operational performance. These services also support new business models and improved revenue streams. Azure IoT Services includes Azure Event Hubs, Azure Machine Learning, Azure HDInsight, and Microsoft Power BI.
Simplify the last mile
For applications that use the least amount of specialized industrial applications for smart buildings, data centers, and IP solutions, hybrid wireless mesh networks provide highly reliable and flexible Internet of Things solutions for monitoring critical data on the ground and in the cloud. Intel NUC, which is easy to set up, configure, and scale, uses a crop networking gateway to provide a scalable, low-cost solution for local analysis and connectivity to advanced analysis tools in Microsoft Azure.
2.00mm Ejector Header Connector
Shenzhen CGE Electronics Co.,Ltd , https://www.cgeconnector.com